Engineering faculty members Jiong Tang and Chengyu Cao are collaborating with global tool giant Stanley Black & Decker to create a methodology to develop software capable of shortening the company’s new product development cycle and enhancing the product performance.
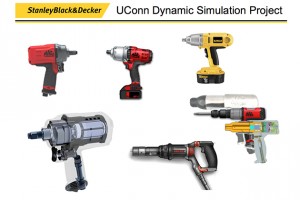
Tang and Cao will analyze the precise mechanism of tools in two of the company’s product lines, impact wrenches and air hammers, in an effort to achieve that goal.
In the development of any new product, the traditional cycle is to design the product, build a prototype, test its performance, tweak the design, build a new prototype, and test it until it meets the need, according to Mark Lehnert, vice president of product development at Stanley Black & Decker, which is headquartered in New Britain, Conn.

“Our aim is to create a dynamic simulation model that can eliminate one or more of the prototype stages,” says Lehnert. “If we can design and test a new product on a computer, we have much greater flexibility to tweak the design, and change the design parameters and materials without sacrificing time.”
A computer could potentially run a simulation in four to six hours, whereas the traditional prototyping cycle can consume up to six months, he adds.
To better understand the tool mechanisms, Tang, Cao, and their graduate students Victor Zhang and David Yoo, are developing a dynamic model using a series of software platforms.
The two-year university-industry collaboration, which began in July 2013, is a multi-phase project, with the first step centering on the careful mechanical analysis of the wrench aimed at revealing the precise action underway when the wrench is operating. When complete, the process will be repeated for the air hammer.
This article was first published in the School of Engineering newsletter, Momentum. It has been edited for length.