You can’t box, package or clone innovation. There aren’t any magic pills, high-tech machines or proprietary software applications to get us to those significant “ah-ha” moments, and no artificial intelligence program, to date, can think as creatively or collaboratively as its human creators. What we can do, however, is lay a proper foundation for allowing people to sharpen their knowledge, skills and experience, all aimed at helping them achieve their potential, guide others and, hopefully, stir those innovative juices.
That, unofficially, is the mission of the newly named College of Engineering (CoE) Innovation Shop, previously casually referred to as the Machine and Electronics Shops. Nicknamed the iShop, it is situated on the ground floor of the Castleman Building, a 6,000-square-foot space for professionally guided hands-on education, creating, collaboration and collegial associations. And while the literal names may partially describe the overall functions taking place in this location, they don’t aptly portray the value, depth of experience and extraordinary experiential learning taking place daily.
The Innovation Shop offers academic and manufacturing support to all CoE students and faculty. Led by four faculty instructors spanning backgrounds in engineering, biomedical engineering, accounting, architecture, military-specification machining, electronics and more, students can gain hands-on exposure and invaluable skills in a wide variety of engineering-related disciplines and fields on their way to a complete engineering education.
Staff Anthony Beatty, Peter Glaude, Joseph Luciani, and Kenneth Premo embrace a holistic approach to innovative engineering. They envision the Innovation Shop as a dynamic, comfortable space for students and faculty to come, discuss ideas, design and create projects and become familiar with the wide variety of manufacturing, design and production tools and equipment available onsite.
Beatty is a product-development engineer. He has extensive experience designing precision medical devices ranging from imaging, to implants, to instrumentation, and bringing them to market under FDA and ISO regulations. The Innovation Shop mission, he explains, is “empowering student innovators through experiential learning,” and he and his fellow instructors embrace their charge, bringing a rich array of knowledge and expertise.
“We see this as a safe, creative and collaborative space for students to get their ‘feet wet’ by becoming comfortable with a wide array of tech and the kinds of tools and machinery they’ll be using or be exposed to after they graduate,” says Beatty. “It’s not necessarily that they have to become proficient in running every type of lathe, milling machine, drill press or CAD system, but being familiar with this equipment and understanding abilities, features and limitations will help them guide projects and better communicate with the manufacturing specialists they will interact with in their future jobs.”
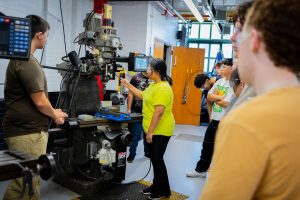
Kenneth Premo, an electrical engineer, is skilled in multiple programming languages, controls, data-acquisition systems and more. He also utilizes his accounting degrees when strategizing budget and business-development plans. One of their team goals, he stresses, is to encourage engineering students to visit the Innovation Shop early in their UConn tenure, so they have time for more hands-on learning, consultation and guidance. Engineering faculty, he says, can help guide newer students to see the Innovation Shop as a valuable, long-term asset.
“In the past, engineering students might visit on occasion, experience an initial orientation or come to us when it’s time to work on their senior design projects,” he explains. “But we see that as missed opportunity – we’d prefer that students become regular visitors much earlier on, and as they grow and learn, assume mentoring roles for other students. That helps build leaders, as well as initial learners, and encourages more collaboration and creative problem-solving.”
Eric Lin ’25 (ENG) is a Computer Engineering student and worked with Premo on developing a printed circuit board (PCB) for his senior design project, as part of a prototype device used for electrochemical techniques.
“It was my first time designing a PCB and I needed all the help I could get,” says Lin. “Ken provided me with helpful resources and videos, guided me at a soldering station in the lab, and walked me through the tools I needed. When I gave him my finalized PCB design to review, he provided constructive tips and suggested improvements, then helped me order the board through a specialized website he had used in the past.”
Lin reflects that without this guidance, his learning curve would have been far steeper. That value-added benefit, says Sean Rescanski ’22 (ENG), who graduated with a degree in Mechanical Engineering and now is a Ph.D. graduate student tech working with the Innovation Shop, is exactly what makes the Shop so useful and important. Rescanski says he worked closely with Glaude, a team instructor and manufacturing engineer, and that the experience helped him tremendously.
“I was lucky to have plenty of manufacturing experience between trade school and working with Pete as a machinist for four years as an undergraduate mechanical engineering student,” Rescanski says. “I also saw many of my fellow ME students struggle during senior design because of a lack of perspective and experience with executing open-ended projects which required manufacturing.
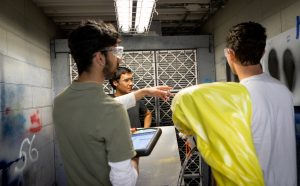
“Early undergraduate exposure to manufacturing and the chance to work on hard projects that require technical skills pays massive short- and long-term dividends to students,” Rescanski reflects. “Additionally, having a space which allows for interdisciplinary collaboration helps students understand how their field fits into the broader picture of engineering and gives them the ability to tackle much more complex projects.”
The fourth member of the Innovation Shop team is Luciani, Design and Manufacturing instructor. His expertise includes rapid prototyping, machining and product design.
“You can’t underestimate the significance of early exposure to process development and DFMA — Design for Manufacturing and Assembly,” Luciani says. “We provide hands-on access to a wide spectrum of services, manufacturing equipment and technology, specific functions or a soup-to-nuts approach that orients students in a bigger-picture way, in addition to helping them think through creative solutions to projects and engineering challenges. Here you can make mistakes, try out different options and get your hands dirty without compromising product development or safety. And everything is done under the watchful eyes and direction of a team that’s been there, done that and is happy to share our expertise and insight.”
The Innovation Shop will sponsor an open house later this fall. To learn more about their services and capabilities, visit the iShop’s site.