
Researchers in the School of Engineering are working with the U.S. Department of Energy to develop advanced coatings for a new energy-producing turbine that produces dramatically lower greenhouse gas emissions than traditional turbines.
UConn is one of nine universities chosen to conduct advanced turbine technology research for the clean and efficient operation of turbines using fuels derived from coal and containing high amounts of hydrogen, according to a U.S. Department of Energy announcement. These high-hydrogen-content fuels are crucial to developing advanced coal-based power generation systems that can capture and store carbon dioxide, a major greenhouse gas.
The University received a grant of nearly $500,000 from the U.S. Department of Energy’s Office of Fossil Energy to pursue the research as part of the department’s University Turbine Research Program. UConn will match the federal grant with a $158,000 investment of its own. The other universities working on the turbine project are: the University of Michigan, University of California-Irvine, Purdue University, Ohio State University, University of North Dakota, Tennessee Technological University, University of Pittsburgh, and University of Texas at Austin.
According to the Department of Energy, the University Turbine Systems Research Program “uses university talent, expertise, and research and modeling capabilities to further advance fundamental gas turbine technology development in the areas of hydrogen combustion, high temperature materials, heat transfer, and aerodynamics.” The research will be conducted over the next 36 months.
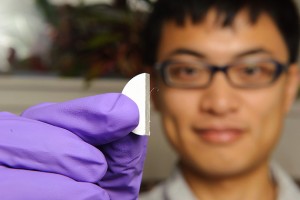
The UConn School of Engineering plans to use the DOE grant to continue its groundbreaking research into the development of advanced thermal barrier coatings for turbine engines using a novel process called “solution precursor plasma spray” technology or SPPS. This process allows for the creation of a unique thermal barrier coating microstructure that dramatically reduces damage from the intense heat found in gas turbines. UConn researchers believe that the coatings developed through the SPPS process are superior to traditional powder coatings applied to turbine engine parts and can withstand more intense heat and strain.
Eric Jordan, the United Technologies Professor of Advanced Materials Processing in the School of Engineering and principal investigator on the project, says UConn was chosen for the work because it is a leader in developing the technology used to create the advanced surface coatings.
“UConn has been the primary developer of the [SPPS] process,” he says. “We started working on it about 12 years ago with Inframat, a Connecticut-based company.”
The Inframat Corp. was created in 1995 by former UConn professor Peter Strutt and his research colleagues in academia and the private sector, with the intent of developing and commercializing advancements in nanotechnology. The new corporation was supported by funding from the Nanoprecision Manufacturing Program run by Connecticut Innovations Inc. Inframat has since become a research leader in advanced thermal spray products and industrial coatings that are used by the federal government. Its headquarters are in Manchester, Conn.
Aside from the novel coating microstructure, Jordan says, another main advantage of the SPPS process is the time it takes to develop a solution.
“It can take up to six months to develop traditional powder coatings, but solution coatings have been developed as quickly as two in a single day,” he says.
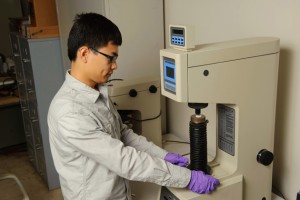
The Department of Energy is seeking UConn’s assistance in developing an SPPS coating for use on a new type of turbine that will burn gasified coal. These new turbines will rely on the coating developed at UConn to protect against the extreme heat that is generated by burning this type of coal. The new turbines will produce far fewer greenhouse gas emissions than traditional turbines, since most of the carbon dioxide in the coal is removed and safely returned to the ground during the gasification process.
“The Department of Energy is committed to advancing cutting-edge research and development into promising technologies that can help America meet its energy needs, remain competitive in the energy economies of tomorrow, and create jobs here in America,” says Charles McConnell, chief operating officer for the DOE’s Office of Fossil Energy. “Projects like this are critical to ensuring the future of clean energy technology.”
A five-member team of scientists will conduct the research, led by Jordan. A member of the Connecticut Academy of Science and Engineering, Jordan has 30 years’ experience in academic research and his work has been cited in about 2,000 journals. Maurice Gell, professor-in-residence in the Department of Chemical, Materials, and Biomolecular Engineering, will serve as deputy program manager. Gell has 27 years of high-temperature materials, experience with Pratt & Whitney, and 16 years of academic research experience at UConn. He holds 20 patents and is the author of more than 125 publications. Many of the oxidation-resistant thermal barrier coatings in commercial use today were developed by Gell’s research group at Pratt & Whitney. Jeffrey Roth, a plasma spray technician with more than 25 years’ experience, and two Ph.D. students round out the team.
Support is also provided by Siemens Corp. and by Pratt & Whitney.